Berk Birand, CEO, Fero Labs, says that by leveraging AI, manufacturers can achieve unprecedented levels of productivity and sustainability – with real-world examples to highlight its impact.
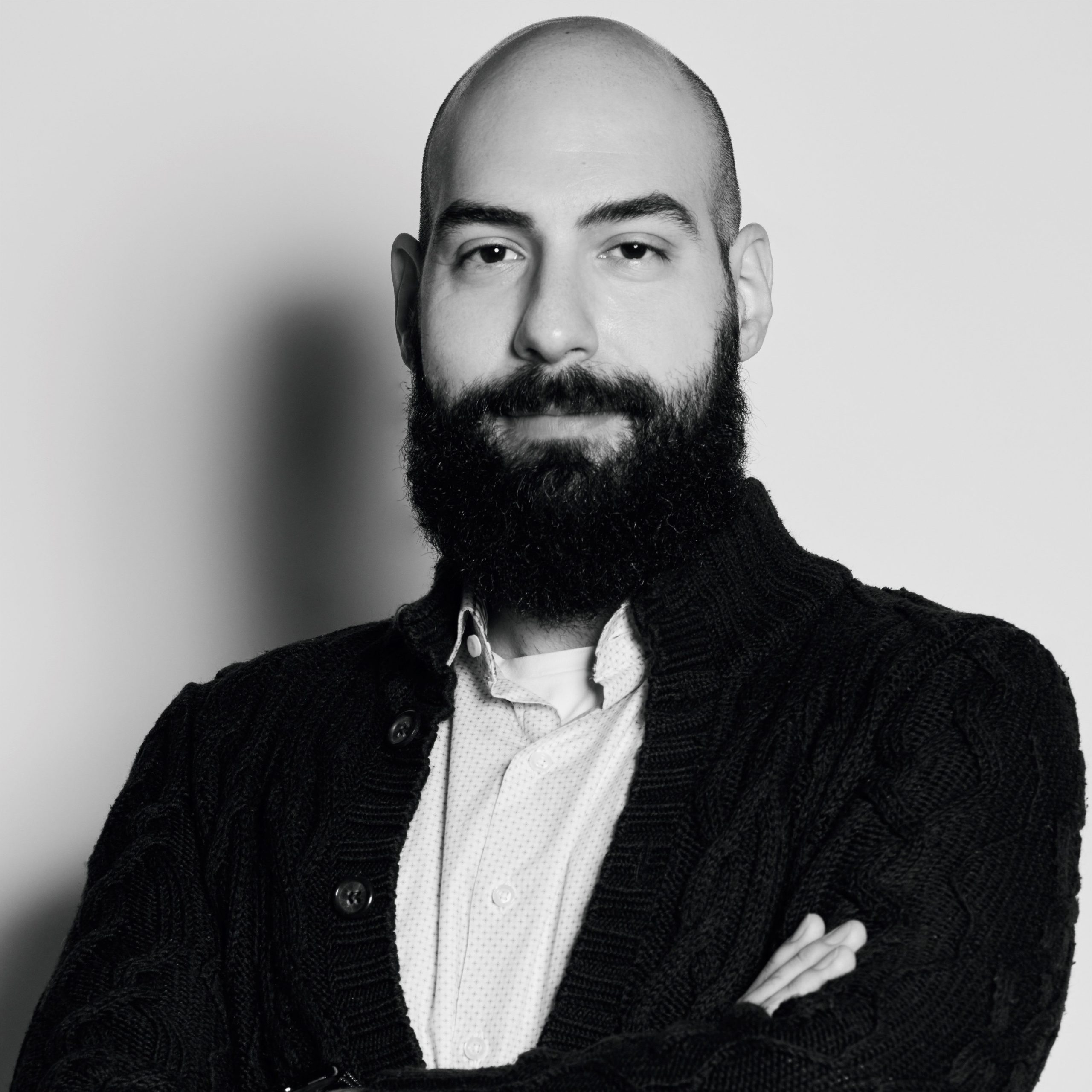
AI is reshaping the industrial landscape, acting as a powerful force multiplier for manufacturing plants to get the most out of their production and the most out of their team. Yet, technological adoption has been slow, with McKinsey reporting that more than 74% of trials never get past pilot stage.
In an era where all sectors of the economy are forced to do more with less, the manufacturing industry must fully digitize by embracing the vast economic capabilities that AI can provide if they are to survive and thrive.
In the steel and chemicals sectors, early adopters of AI are enhancing efficiency, reducing costs, driving innovation, decarbonizing and optimizing these outcomes in real time.
Here’s a detailed look at how AI is transforming traditional practices in these industries today, with real-world examples from inside the plant to highlight its impact.
Predictive Maintenance
Companies like Tata Steel and BASF use AI to predict equipment failures by analyzing sensor data. AI models forecast the remaining useful life of components, enabling timely maintenance. Tata Steel has reduced downtime by 20% and maintenance costs by 15%, while BASF has seen a 25% reduction in unplanned downtime and 20% lower maintenance costs. AI acts as a force multiplier by turning reactive maintenance into proactive, data-driven strategies.
Quality Control and Defect Detection
ArcelorMittal and Dow Chemical utilize AI-powered computer vision systems and real-time data analysis to inspect products and detect quality issues early. These systems detect defects faster and more accurately, reducing scrap rates and rework costs. Dow Chemical’s AI models identify deviations in product quality early, significantly cutting waste. Here, AI serves as a force multiplier by exponentially increasing the speed and accuracy of defect detection.
Process Optimization
POSCO and DuPont have implemented AI to optimize their production processes. AI continuously adjusts parameters in real-time, improving efficiency and reducing costs. POSCO achieved a 5% increase in production efficiency and a 10% reduction in energy consumption, while DuPont reduced raw material consumption by 8%. AI amplifies the impact of process optimization, making it more dynamic and precise.
Anomaly Detection
Companies like Baosteel and Dow Chemical use AI to continuously monitor production parameters, detecting anomalies in real-time. This allows for immediate corrective actions, reducing quality issues and process disruptions. AI’s force multiplier effect ensures quicker identification and resolution of potential problems, maintaining smooth operations.
Energy Management
Thyssenkrupp and BASF use AI to analyze energy consumption patterns and optimize energy use in real-time. This has led to a 10% reduction in energy costs and more sustainable operations for both companies. AI enhances energy management, making it more proactive and effective.
Profitable Sustainability
Using AI, profit and sustainability are no longer mutually exclusive and quality doesn’t need to be compromised. Steel manufacturer Gerdau, has used AI to significantly reduce alloy costs by $3 per ton. This decreased their annual volume of alloys, resulting in a Scope 2 and 3 reduction. AI’s role as a force multiplier is evident in its ability to reduce waste, maximize energy consumption, and advance sustainability initiatives.
Data Integration and Analysis
JFE Steel and Shell Chemicals use AI to integrate data from multiple systems, providing a unified view of operations and enabling advanced analytics. This has enhanced decision-making and operational efficiency. AI’s integration capabilities multiply the value derived from disparate data sources, enabling more informed decision-making.
Real-Time Monitoring and Control
Voestalpine and ExxonMobil Chemicals use AI to process real-time data from IoT devices, providing instant feedback and automated control of equipment settings. This maintains optimal performance and improves process reliability. AI’s real-time capabilities act as a force multiplier by ensuring continuous, automated process control.
Enhanced Decision-Making
US Steel and Chevron Phillips Chemical leverage AI for data-driven insights and decision support. AI enables faster and more accurate decision-making, improving strategic planning and operational outcomes. AI’s advanced analytics serve as a force multiplier by providing deep, actionable insights that drive more informed decisions.
Labor Efficiency
SSAB and Bayer use AI to optimize labor schedules and task assignments, ensuring the right personnel are deployed for specific tasks. This has improved labor productivity by 15% in both companies. AI acts as a force multiplier by optimizing human resources, enhancing productivity, and ensuring better utilization of skills and cross-functional communication in a busy plant.
These examples demonstrate AI’s profound impact, making it an invaluable tool for data scientists and industrial operations. By leveraging AI, manufacturers can achieve unprecedented levels of productivity and sustainability, positioning themselves for a competitive edge in the global market.