Fred Baumann, GVP, Industry Strategies, JDA Software, explains the four key strategies to consider when taking steps to increase supply chain readiness in the manufacturing industry as companies prepare for digital innovation.
Manufacturing supply chains are at an inflection point. Optimisation is moving from node to network, planning and decision frequency is changing from periodic to real-time and the supply chain itself is evolving from ‘one‑size-fits-all’ to a market segment size of one. The rules of the game are changing and with it, supply chains are becoming centre stage in developing the next stage of competitive advantage.
Historically, the effectiveness of manufacturing supply chains has been measured through functional efficiency alone. While, at best, this may result in efficient functions, it creates inefficient organisations. This inefficiency is then amplified as the supply chain reaches out to connect with its customers, suppliers and beyond.
With poor visibility of data across the end-to-end supply chain and a historic scarcity of predictive analytics and decision support tools, it has been difficult to move beyond a functional siloed view. However, over the last few years this situation has changed and digital solutions have emerged that have the potential to address both these challenges.
JDA recently worked with Warwick Manufacturing Group (WMG), The University of Warwick, to create the Supply Chain Digital Readiness Report where 180 major manufacturing companies in Europe took part. The report defines digital readiness across four key levels. So just how close are manufacturers to digital supply chains?
The journey is underway
The research reveals that European manufacturers are at an early stage of the journey – see figure below. Only 13% have so far reached level three readiness: dynamic end-to-end supply chain optimisation supported by an advanced analytics capability, starting to leverage ML and AI. 52% were at level two readiness: leveraging some specialist analytics tools to support functional optimisation. 35% were still trying to get visibility of data and were using simple analytics tools (e.g. spread sheets) predominantly for reporting. By 2023, level three readiness is predicted to more than double to 31%. However, the average level of readiness is only predicted to increase by half a level from 2.3 to 2.8.
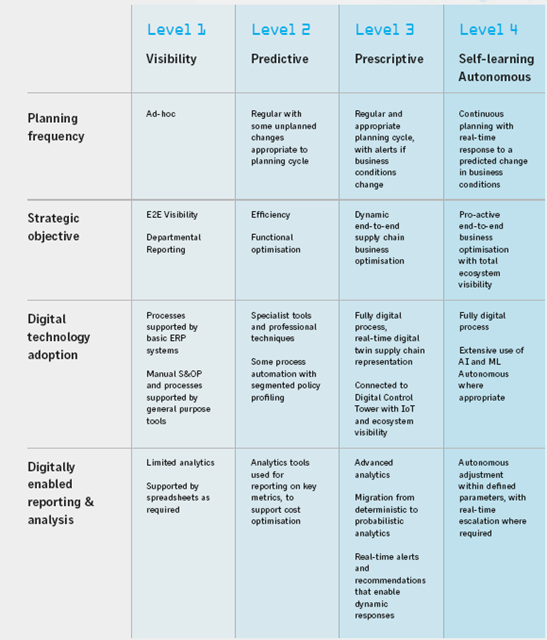
While there’s no silver bullet to increase supply chain readiness, there are four key strategies to consider:
1. Enhance visibility and optimise core supply chain processes
Supply chains consist of five core processes; planning, procurement, manufacturing, logistics and return. The reality for many manufacturers is that they fail to use the data they currently have to optimise these core processes in a holistic way.
Therefore, the first step in improving digital readiness is to enable end-to-end visibility for supply chain optimisation by capturing data stranded across various legacy systems, such as Enterprise Resource Planning (ERP) and disparate planning and execution solutions. The critical step is to recognise the importance of this data and develop governance processes to maintain its integrity. The next step is then to improve data capture, in those areas where having that data could make a difference. The growth of real-time data from social, weather, IoT and other sources requires a platform that can ingest these signals in real time. Advanced analytics and decision support systems can then be utilised to improve efficiency here. This enables manufacturers to make the most of what they currently have to sustain their legacy business. It builds a foundation for operational excellence and can free up cash to enable the business to invest in new ways to compete.
2. Adopt a supply chain business process orientation
The second stage is arguably the most difficult but is also the most crucial for manufacturers to move beyond functional optimisation. It requires them to give equal importance to managing the supply chain as an end-to-end business process, as they do to new product development and customer relationship management.
This requires a change in organisational structure and aligned metrics, to overlay a business process perspective across the classic functional structure. This is critical, as whilst they draw on functional resources, they break down the boundaries as they seek to optimise the business around strategic rather than siloed functional goals.
3. Proactively mitigate risk to the supply chain by leveraging new digital innovations
There are numerous technologies, such as AI and ML, that manufacturers can use to improve individual aspects of their supply chain. It is important to create ‘proof of value’ use cases in which these technologies can be trialled. Proof of concept initiatives that take a subset of the network and products can enable companies to build their business case based on their operating environment. Good research can limit failure, but manufacturers should not be afraid to ‘fail fast’; assuming they have good processes in place to capture the learning. One way to de-risk the digital technology pilot is to be clear on what is being piloted and document success criteria.
To minimise risk and maximise learning, current capabilities should be developed in a step-by-step way. Apply new technology to an existing process or a new way of working with existing technology, but not simultaneously. In this way, if the pilot succeeds or fails, the reason is clear. It also provides a pathway for moving up the learning curve for new technologies where applications that provide benefit over current technologies are limited. It will help create first mover advantage when beneficial applications for the technology become evident.
4. Explore new business models
We are in a transition point between two stages of our industrial evolution. The economic benefits of consumption-driven growth are beginning to be outweighed by the environmental and societal costs. This is redefining business models to encourage greater sharing and consideration of how ‘stuff’ can be retained in its highest possible value state for as long as possible. It is seeing a shift from the provision of products to services and is supported by a shift in the design of supply chains. Circular supply chains that incorporate re-use and recycle on the front-end of product design is a prime example of new business model thinking.
Digital technologies are a key enabler to these new business models that are disruptive and often in direct conflict with the legacy business model upon which the short-term success of their organisation depends. This is a great time to be a small organisation that can leverage the benefits of a more agile structure. For large legacy businesses, consider setting up a separate organisational entity that has the freedom to explore the art of the possible and build the business model of tomorrow.
Start your journey now
We are in the midst of massive change; a change that will see supply chains become the core of how organisations compete. Moreover, the intelligent use of digital technologies will enable new models of economic growth and productivity. To achieve this, manufacturers should be making more effective use of their data – especially to support end-to-end-to-ecosystem visibility alongside an increasing use of AI to get ahead of disruption and opportunity. Ultimately, to keep customers happy, manufacturers need to find the appropriate blend of digital innovation to achieve a new generation of profitable and personalised efficiency.