Rosti Group reduces device downtime by more than four hours per device, per month and can now deploy applications 20 times faster with SOTI MobiControl.
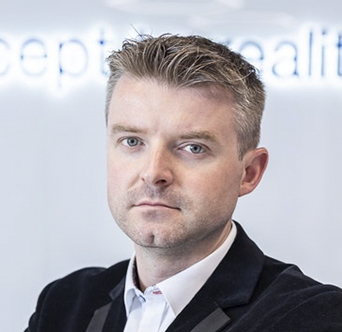
Rosti Group (Rosti), a global expert in plastic injection and contract manufacturing services, reported a 40% increase in productivity following the successful implementation of SOTI MobiControl, part of the SOTI ONE Platform.
With production sites in the UK, Europe and Asia, Rosti has a distributed workforce to provide the best service to some of the world’s leading businesses in the packaging, consumer appliances, medical and automotive sectors. Rosti produces more than 400 million beer can widgets annually at its 2,400 square metre facility in York, as part of its expanding UK operations.
With IT support and operations centrally located in Poland, managing the hundreds of devices, rugged handsets and scanners across its global locations proved difficult for Rosti. IT personnel would spend two to three days travelling from the centre in Poland to fix device issues overseas, which resulted in lower productivity for both the support team and device user.
Additional challenges included excessive device downtime, concerns around security, lack of technological depth across regions as well as numerous data collection processes reliant on outdated paper-based methods. These challenges created the need for a shift to an Enterprise Mobility Management (EMM) platform to streamline operations.
After a successful proof of concept, Rosti leveraged SOTI MobiControl to revolutionise its device management processes. Streamlined app installations achieved a 20-fold increase in deployment speed while maintaining robust security, which in turn boosted productivity. SOTI MobiControl’s Lockdown feature secured vital data and remote software updates, ensuring devices remained current with the latest security protocols, in line with device manufacturer warranties, as well as enhancing resilience against malware threats and fostering a secure, productive environment.
Since implementing SOTI MobiControl, Rosti has experienced a significant improvement in flexibility and speed of executing its updated business standards across its mobile operations. The company benefitted from reducing downtime caused by hardware issues by more than four hours per device, per month. Now, Rosti’s IT team can efficiently trace device locations and access hardware warranty information for device updates and replacements when necessary.
“The ability to troubleshoot tech and software remotely is critical to the success of a distributed workforce. Without it, the most common consequence is an increase in device downtime, which can tank productivity and revenue, jeopardise customer trust and frustrate employees,” said Faki Saadi, Director of Sales, UK and Ireland, at SOTI. “An advanced central management tool like SOTI MobiControl allows businesses to save time and money. IT teams can solve issues quickly and efficiently without needing the device in their hands. Apps can be deployed in seconds and updates are managed with ease, speed, accuracy and security.”
“By deploying SOTI MobiControl across our entire global device fleet, we have significantly enhanced our governance model, streamlined the application and firmware update procedures and elevated the quality of support we offer to our clients,” said Andrzej Chojnowski, IT Director Europe, Rosti. “SOTI has revolutionised our ability to deliver the necessary resources to sustain our entire business. As a result, our organisation has experienced a remarkable increase in cost-effectiveness and overall performance.”
We asked Andrzej Chojnowski, IT Director Europe at Rosti, further questions to find out more about the project.
Could you elaborate on the specific challenges Rosti faced in managing its distributed workforce’s devices prior to implementing SOTI MobiControl?
Before working with SOTI, we were starting to feel the strain, both from a cost and time perspective, of sending IT personnel to a location every time a device issue occurred. This could sometimes take up to three days and we would often have to bring in external help which as you can imagine, became rather expensive.
This was our only option at the time, as we lacked a clear view over our devices and the ability to remotely troubleshoot issues. Depending on the severity, it could stop service delivery completely, a problem we couldn’t afford especially as the business continued to grow. This lack of visibility also meant we couldn’t identify root causes. As a result, we couldn’t proactively plan for wider difficulties because we didn’t have the data to tell us if this was an isolated issue or if it might impact our wider fleet. These are challenges we’ve been able to address with SOTI MobiControl and our IT operations have run much smoother since.
How has the implementation of SOTI MobiControl impacted Rosti’s productivity and operational efficiency, particularly in terms of reducing device downtime and streamlining hardware issue resolution?
Resolving problems quickly and limiting device downtime were significant obstacles for us before this project began. Now we have access to a single dashboard that lets our IT team see every piece of technology connected to our network, across every location globally. This means we can review a device’s status in real-time, including what software and firmware it’s running, any performance issues and reliability metrics. This makes it a lot easier to troubleshoot issues before they develop into major problems. SOTI’s software also makes recommendations in the platform to update software and hardware which helps us better manage our manufacturer warranties. We’ve noticed this is helping us to be more efficient by reducing support costs.
Could you describe the process of transitioning to a more streamlined Enterprise Mobility Management (EMM) platform, and the role SOTI MobiControl played in this transition?
SOTI’s EMM solutions works with all global operating systems and devices. This meant everything could be easily integrated into the platform, helping the transition greatly.
Having a more streamlined management solution has taken a lot of the mental burden off our employees, as well. For example, our operating systems often need routine updates and previously, teams needed to keep a record to remember to review and distribute software. This is now done automatically. This means everything is scheduled ahead of time, regardless of the time zone. It’s the small elements that alleviate time pressures for our staff and ensure that our users experience minimal downtime.
What are some key features of SOTI MobiControl that have proven most beneficial to Rosti’s IT operations and support functions?
There are three main features that have made an impact at Rosti. Firstly, the ability to manage and support issues remotely has had a notable impact on savings for both time and cost. Secondly, the breadth of device diagnostics that SOTI MobiControl gives us has been very useful. Our teams are now equipped to identify problems fast and deal with them efficiently. Even better, we can use the intelligence provided by SOTI to predict problems before they happen.
From a security point of view, the lockdown feature has been handy. This allows us to restrict access of certain applications and device features depending on a person’s job function. We all understand the threat landscape is becoming more hostile and hackers are continuing to target businesses as a result of the increasing volumes of sensitive data that many organisations now store. By ensuring that everyone only has access to what they need, we’re able to minimise unnecessary risk.
In what specific ways has the deployment of SOTI MobiControl across Rosti’s global device fleet enhanced the company’s governance model and client support capabilities?
SOTI MobiControl has ensured we can send out automated training reminders to all of our staff, to ensure they are up to date on the latest compliance requirements. We’re also able to easily distribute device security patches to ensure all our hardware is better protected against the latest threats. The additional data we now have access to, also makes it easier to pull the necessary information for any reports or audit requirements we may need to submit.
In terms of client support, we have never been in a stronger position to ensure our users receive a smooth experience because of new remote support capabilities, faster diagnostic tools and the ability to stop a device issue in its tracks before it impacts the wider fleet.