Digital Twins have long been an essential component in the design and management of Smart City projects across the Middle East – from NEOM in Saudi Arabia to a digital-twin of Dubai as one of the emirates in the metaverse for the UAE and Qatar’s sprawling Hamad International Airport. We speak with Sumanta Roy, TCS Vice President and Regional Head of Middle East and Africa on the technical sophistication and non-existent margin for error of these major projects mean a form of twin technology is imperative to forecast problems, simulate scenarios and effectively plan outcomes.
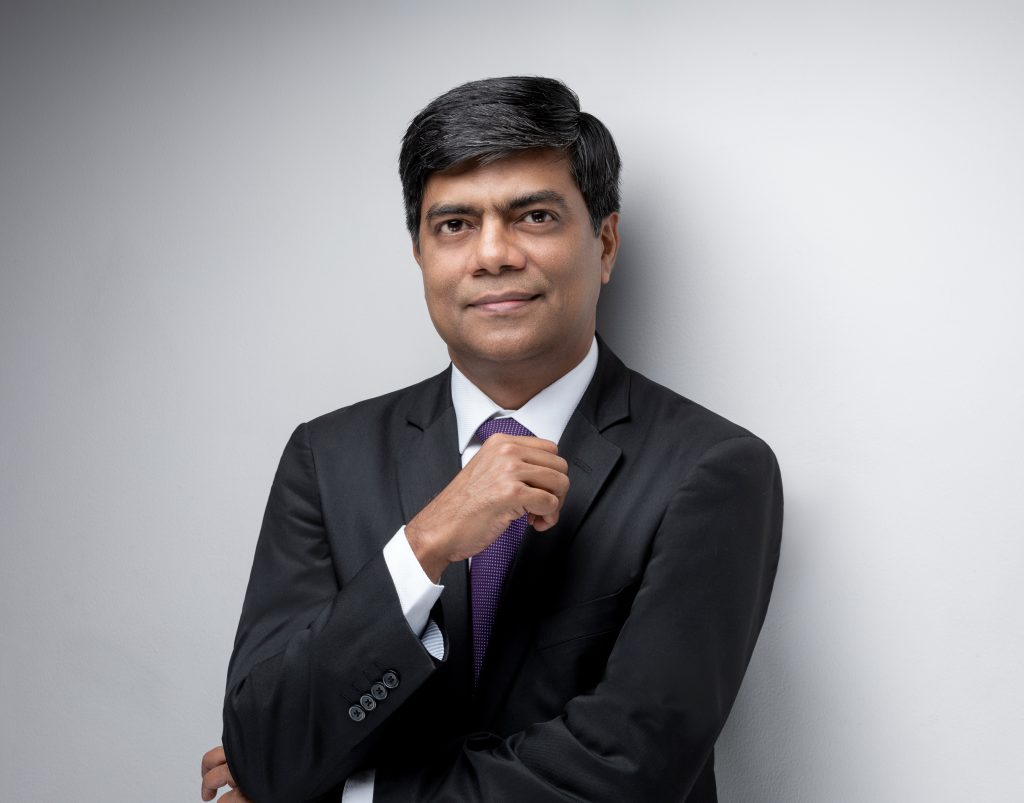
Yet the massive value provided by twin technology isn’t reserved only for the region’s fast-moving urban development projects. Digital Twins also represent a major opportunity to galvanize the region’s industrial sector and accelerate its growth.
The Middle East is seeking smart or digital manufacturing capabilities that will open doors to economic growth and improved supply chain resilience. Today, smart manufacturing is the need of the hour to monitor and optimise production processes – cutting costs while ensuring maximum performance. This type of intelligence-driven manufacturing will enable the automation of operations and the identification of opportunities to improve performance through data analysis.
Digital Twin technology has many significant roles to play in smart manufacturing.
Improved predictive maintenance
In manufacturing, visibility over all processes is key. Uncertainty can be common in manufacturing systems that do not integrate technological approaches such as Big Data analytics, simulations and systems integration to improve performance. This uncertainty can manifest itself as an equipment breakdown, changes to the product or service lifecycle, or the fluctuating productivity of processes.
With a Digital Twin, visibility is enhanced in industrial processes and the uncertainty is removed. These two key challenges, solved with a Digital Twin, improves predictive maintenance in manufacturing. Companies across a variety of industries including automotive and construction have reported that such advantages are only possible with a Digital Twin. This is because a digital copy of industrial process grants an unprecedented level of transparency into hardware, allowing users to proactively fix equipment before it breaks down, resulting in maximum productivity, minimised costs and improved revenue.
For instance, Tata Consultancy Services (TCS) built a model for a Japanese client based on the Digital Twin technology. The customer highlighted a need to optimise the operating conditions for its coal fired power plants with a model that could continuously monitor performance and raise any red flags. TCS developed a predictive Digital Twin model based on historic and real time operating data that uses algorithms and Machine Learning to improve performance. The client recorded reduced fuel consumption resulting in lower costs, but also identified an opportunity to optimise its boiler settings for reduced carbon emissions. Meanwhile, faults could now be detected in the plant 12 hours in advance with 85 percent accuracy.
Bridging the gap between humans and machines
While smart manufacturing is run through technological processes, there is still the need for human presence to assist Machine Learning, which Digital Twins enable by connecting machine and human. An employee sitting thousands of miles away from a physical machine can monitor its performance through the digital counterpart, which replicates the conditions and performance of the physical machine. Engineers monitoring the digital model can eliminate errors by removing points of failure. Manufacturers aiming to receive feedback from customers on industrial processes can enable the same via the Digital Twin with the help of Internet of Things (IoT).
For instance, leading developers in the Middle East region such as Saudi Arabia’s Red Sea Development Company are using Digital Twin technology to monitor real-time information, allowing facility owners to measure user experience. Those generally monitoring a building’s temperature and air quality can also use the same data to schedule maintenance and create emergency scenarios in the cases of a fire or flood. Another example is of how the US Air Force has extensively used Digital Twins to design and build aircraft prototypes in a little over 12 months, when previously the task took years. Digital Twins fuel this accelerated design and manufacturing cycle by improving collaboration and workflow between engineering, manufacturing and quality control teams. Together, they can analyse any evident problems across the process, reducing manufacturing downtime and increasing productivity.
Just like that, the Digital Twin technology allows a broader set of professionals from far and wide to enhance and improve the processes of the physical counterpart. Significantly, the Digital Twin can be accessed 24/7, allowing technicians to improve collaboration between teams and operational efficiency among international companies.
Accelerated speed of product development
Product development speed is a key indicator of the effectiveness of industrial operations. Time-to-market has become a competitive challenge and a powerful point of differentiation for manufacturers worldwide as they seek to manage innovation in fast changing environments.
With a Digital Twin, manufacturers can troubleshoot instantly during the product development process, rectifying and diagnosing issues with great efficiency. Additionally, even post-product release, a Digital Twin can act as a reflection for how well a product is performing in the market and a tool for calculating its usage ratio among customers. Statistics and data are fed into the product development and manufacturing process to make improvements that in turn, boost profit margins, customer satisfaction and market share.
The Middle East has much utilised the Digital Twin model in launching various successful Smart City projects. Looking ahead, incorporating this very same model across the region’s industrial sector will open doors to vast economic growth and opportunity.
As a matter of fact, the complexity of goods, services, processes and production will lead to a continued increase in the deployment of Digital Twins.