Stephen Reynolds, Industry Principal Chemicals, AVEVA, explains how a digital twin, which replicates company assets in the cloud, helps to design low carbon processes and plants.
In recent decades, digital technology has been successfully used to optimise plant operations, increase production, or reduce costs. But today, field-proven software can go so much further – allowing you to radically optimise your business while also calculating greenhouse gas emissions, GHG and minimising energy consumption, helping you to address Scope 1, 2 and 3 emissions.
- Scope 1 covers emissions from sources that an organisation owns directly – for example from burning fuel in a cracking furnace.
- Scope 2 are emissions that a company causes indirectly when the energy it purchases and uses is produced. For example, the emissions from the generation of the electrical power used to power the industrial plant would fall into this category.
- Scope 3 covers emissions that are not produced by the company itself, but by those that it’s indirectly responsible for, up and down its value chain.
As complex it can be to monitor and reduce GHG emissions, you can start simple and get some immediate results. For example, by using digital technology to break down information silos, it is possible to covert raw plant data into contextualised information to enable the quick calculation of GHG emissions, energy consumption and carbon intensity and have some quick wins.
Through partnering data with different advanced applications, you can enable digital engineering and operations to positively transform your plant efficiency and turn those initial quick wins in significant medium and long term benefits.
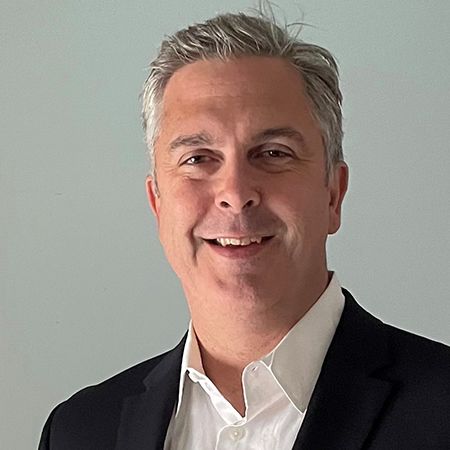
Leveraging the power of the digital twin
Embarking on a digitisation strategy allows you to boost operations, increase asset reliability and futureproof your facilities. A digital twin, which replicates your company’s assets in the cloud, empowers you to make informed decisions on how to best optimise the engineering and design of low carbon processes and plants.
Ultimately, your company is empowered to rigorously contextualise data to help modify your plant’s carbon footprint and manage carbon off-sets and credits – now and into the future.
A Lifecycle Digital Twin tech stack runs your plant in the cloud, converting all its raw data into valuable information to drive carbon intelligence. The combination of data fed into models and analytics – displayed through simple self-serve systems – allows your company to improve operational set points and automate power source selections, reducing emissions and energy consumption.
The first step is certainly having visibility of the carbon footprint.
Digital twin for operations
The digital twin runs a parallel operation to your plant in the digital environment. When it is combined with real time operational data it is able to predict behaviour with accuracy through first principle models and artificial intelligence, AI. These insights then give your teams a window into ways to improve your processes and optimise operations.
A possible approach is energy and emissions management through rigorous modeling to calculate your emissions reduction potential to stabilise and optimise operations. The ‘reduction potential’ informs your teams of the true actionable gap that can be addressed and the limits that can be reached.
Improving the energy mix to maximise your use of clean energy is desirable but not every plant has this option. If your plant has this flexibility, you can use optimisation models to automatically maximise the use of clean energy depending on your plant operating conditions.
Managing upstream and downstream emissions is not an easy task.
Improving reliability
The next step is to improve asset reliability to minimise excursions. Many industrial processes generate more GHG emissions during startup and shutdown procedures, not to mention during accidents, so minimising or eliminating unplanned downtime is critical for keeping your carbon footprint under control.
Artificial intelligence, AI and machine learning, ML models enable early warning notifications that can prompt your staff to act in time of preventing unplanned shutdown and accidents. To take a step further, you can add inferences from rigorous models and calculate the RULE, Remaining Useful Life Estimation, adding predictions accuracy and anticipating notifications even further. This approach combined with an asset strategy optimisation can ensure maximum reliability at minimal costs.
Modifying plants
What is more, to be able to address your carbon footprint challenges, you will need to speed projects from concept to full capacity production. For the engineering and building stages, companies that adopt a data-centric approach with a rigorous lifecycle simulation see the best results. A unified approach allows your engineers to quickly evaluate hundreds of scenarios and optimise the project design according to your goals.
The latest technology also allows you to minimise project risks and ensure your plant is delivered on budget and schedule with an effective handover to operations. This is a critical aspect for maximising the return of your investments in digital technology.
If you have a reliable access to your plant data and effective modeling capabilities, you should also be able to identify if an upgrade is required to manage your GHG emissions and energy usage. So the unified approach can be used for greenfield and brownfield projects.
By combining your operations and engineering data, you’ll be able evaluate options to upgrade your assets to even further reduce your GHG emissions, or be able to incorporate flexibility in the energy mix so clean energy usage can be maximised.
You want to make sure you can extend the benefits of your digital investment in the engineering phase by ensuring the digital twin is properly handover to operations. When the data delivered at the end of the project can be connected to real time operational data, it can be used to guide further improvements on the plant´s operations and maintenance.
Companies struggle to access relevant data that exists, and make it meaningful to users outside operations.
Extending the digital twin benefits across the value chain
The biggest challenge that industrial companies will face is probably to address scope 3 emissions. Managing upstream and downstream emissions is not an easy task.
Currently, companies struggle to access all the relevant data that exists, aggregate it to see the bigger picture, and make it meaningful to users outside operations. And it can be expensive and time-consuming to share data with colleagues and trusted partners.
The first step is certainly having visibility of the carbon footprint. Data sharing across your ecosystem can be beneficial to your company so as to suppliers, customers and partners. Only with full visibility companies can identify the need to purchase carbon credits and also carbon negative options.
This can be addressed with a fully managed cloud-native solution that enables knowledgeable experts who can enrich data streams with metadata and context to help other users understand and make sense of the data. From this it´s possible to create a master planning to develop a roadmap for net-zero. Using data to make better decisions is more and more a core function of business and society. Data is increasingly helping us solve complex problems such as managing and optimising resources to address scope 3 emissions.
Beyond managing data of your value chain, CAPEX projects will be required to build the critical infrastructure to support carbon capture and underground storage, CCUS , green hydrogen production and utilisation and the circular economy. In this case, the value of a digital approach is even higher as more agility and collaboration among multiple stakeholders are required.
Data sharing across the ecosystem can be beneficial to your company so as to suppliers, customers and partners.
Empowering the connected workforce
Finally, we need to remember that none of this is possible without duly empowering the workforce. By digitally enabling our teams, they will learn faster, work smarter and hence have greater insights, leading to better productivity and an improved work-life balance.
Digital technology is the number one enabler for engineers in the office, operators in the control room, field workers on the plant floor, anytime-anywhere remote workers and, of course, the leadership team which requires deep 360 degrees visibility into the enterprise.
Cloud-enabled and AI-driven applications are critical to enabling the workforce and attracting and retaining talent to the industrial environment. The digital twins of the future will empower low-carbon remote working, safe and productive working styles, real time carbon insights, and augmented decision making for optimised carbon footprints.