Process and discrete manufacturers are being forced to rethink how they operate faced with current levels of uncertainty created by geopolitical events, supply chain disruptions and reactive consumer behaviour. Executives from AVEVA, Epicor, IFS, share their comments.
Manufacturers are no strangers to dealing with turbulent market conditions, however the current global landscape is a sea of uncertainty that can sink even the most buoyant of companies. That said, new technologies, improved planning and better use of data have created huge opportunities for companies to adapt and become more resilient.
Plants that want to survive and thrive in a world of economic and supply chain curve balls are realising that the operational concept of efficiency must also be paired with an ethos of responsiveness. In this emerging industrial mindset, manufacturing plants must be efficient whenever possible and responsive when necessary.
Black box
While the business has many gears in its gearbox, the manufacturing plant is usually stuck in just one: efficiency. To maintain profitable margins, the supply chain strategy often revolves around insulating the plant from external volatility. In theory, protecting the process within the plant using a combination of inventory buffers, lead times, and supplier policies allows the plant to focus on a singular goal of increasing efficiency.
But this led to an unfortunate side-effect. The protection from external variability created an insular, within the four walls mindset. As long as production targets were met, corporate continued to treat the plant as a black box. This lack of visibility makes it difficult to engage the plant in modernising the supply chain strategy to achieve greater agility and resilience.
Just like drivers use a gearbox to adapt to different road conditions, businesses need different gears to understand, plan and execute during dynamic, and disruptive business conditions. An agility-focused approach seeks to synchronise the plant with the supply chain strategy whenever it changes gears so it can quickly adapt to changing conditions.
“In other words, the plant becomes more flexible to make changes as conditions warrant. When the plant is agile, it becomes a shock absorber for external volatility,” says Sree Hameed, Consumer Products Industry Strategist at AVEVA.
The responsive, gear driven mindset absorbs shocks from supply disruptions and is able to adapt to changing demands. Supply chain condition changes such as raw materials shortages, logistics issues, or demand spikes can have a massive impact on the manufacturing plant.
While these may be hurdles for some plants, the ability to rapidly adapt to changing supply chain conditions turns those hurdles into opportunities. Quick changeovers allow brands to capitalise on market conditions and run at maximum capacity.
AVEVA’s internal research found that companies changed gears using the following eight levers in their business and supply chain strategy: inventory, capacity, time, segmentation, price, relationships, information, and cash.
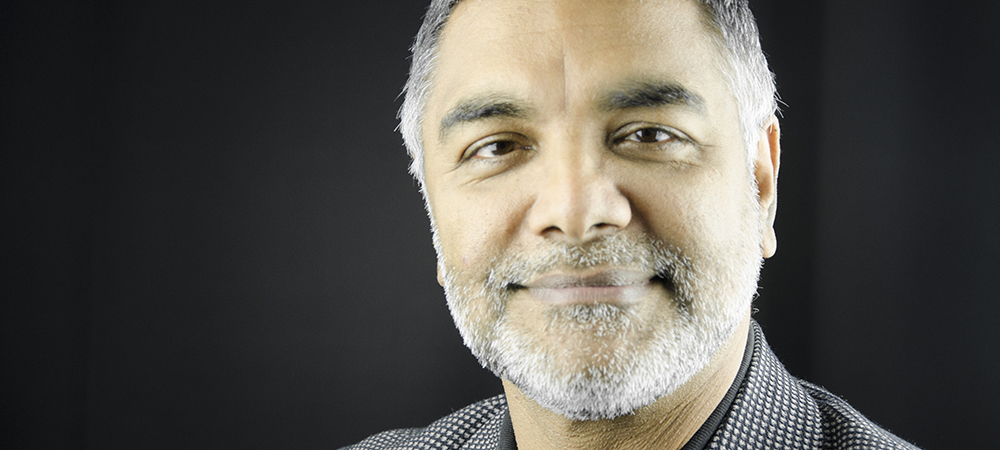

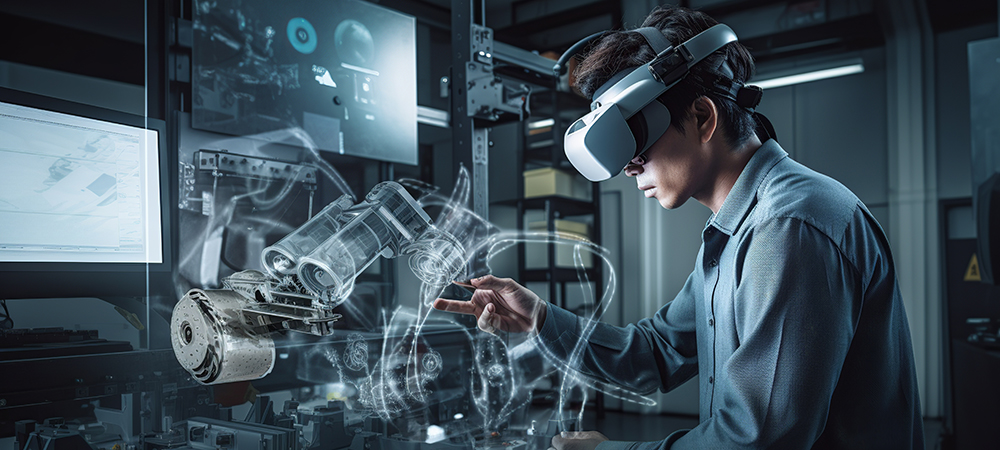
ESG
ESG, as a measurement of a company’s environmental, social, and governance initiatives, has become an essential component of how organisations are assessed and valued, by investors, partners, customers, and employees alike. For manufacturers, the primary focus at present is on the environmental, with the mandate to show progress towards decarbonisation.
Manufacturers voluntarily comply with reporting even when this means dealing with a complex set of reporting regulations, ratings, and disclosure frameworks. In an IFS Sustainability focused customer day, attendees indicated that they typically adhere to three main reporting standards and frameworks: the Global Reporting Initiative, the EU’s Corporate Sustainability Reporting Directive, and the CDP Climate Change Programme. In addition, we also see commitment to the Science-Based Target Initiative, and the Corporate Net-Zero Standard.
“At present we see most manufacturers find it difficult to track scope 1, 2 and 3 emissions. This is mostly due to the fact they are still manually collecting these metrics from within their organisation across entities and different systems while using Excel as a repository and analysis tool,” says Maggie Slowik, Global Industry Director, Manufacturing, IFS.
The coming years will see manufacturers investing in technology in earnest, to help automate and ingest consistent, comparable, and reliable carbon metrics as part of their enhanced ESG disclosures.
Data deluge
“Manufacturers are realising the importance of their data, and how it is, or will run their decision making in real time. New positions are being created for data scientists, or chief data officers, whose role is to understand the data and how it is used,” says Andrew Burton, Global Industry Director, Manufacturing, IFS.
They will be responsible for the accuracy of the data and to understand where the data is coming from and its impact on the day to day running of the business.
As the integration of applications and machines progress the amount of data being collected is increasing exponentially. Not all new connected machines are being used in manufacturing. However, it does show that machines and devices being connected to the Internet and each other will be generating huge amounts of data.
This data must be understood, controlled, managed, and checked for accuracy as this data will form the basis of real time decision making. This will need new skills that are not currently employed in many manufacturing companies.
Cloud ERP
“Cloud ERP is indispensable in ESG journeys of all scales. Manufacturers get to scale up and diversify their capabilities, ensure minimal business disruption, and reduce energy consumption. They get to deliver hybrid working practices and enhance the employee experience by enabling staff to monitor warehousing and other production processes through the cloud,” says Vibhu Kapoor, Regional Vice President, Middle East, Africa and India, Epicor.
The entire ecosystem can be governed in part by advanced AI that provides a range of insights on everything from logistics to inventory management.
Businesses face an ongoing problem of how to adequately measure and embed sustainability along the supply chain. Cloud ERP can help here too. It consumes supply-chain data and uses business-intelligence capabilities to work out the true cost of compliance.
Through these insights, the enterprise can move quickly to minimise disruption to sourcing or distribution. It is abilities like these that allow businesses to find a middle ground between profitability and affordable products for customers.
Sustainable supply chains are the future. To be part of that future, manufacturers need accurate data on the quality of a product, as well as its bill of materials, current location, and all its past, present, and future locations along the chain. The business must understand everything that went into making a product and the potential for it to be remade, reused, or repaired, as well as everything about the processes behind every link on the chain.
What will be the impact of a stock shortage? What are the trends in materials pricing? How do we expect the logistics sector to behave in the next weeks, months, or years? Weighing sustainability against cost is a lot easier with ERP because it can convert real-time data into an insightful worldview that drives agility and resilience for the business.
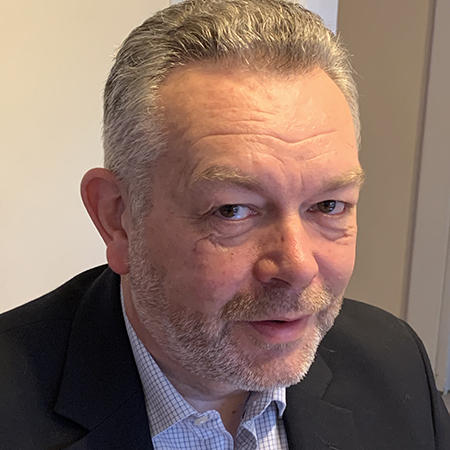
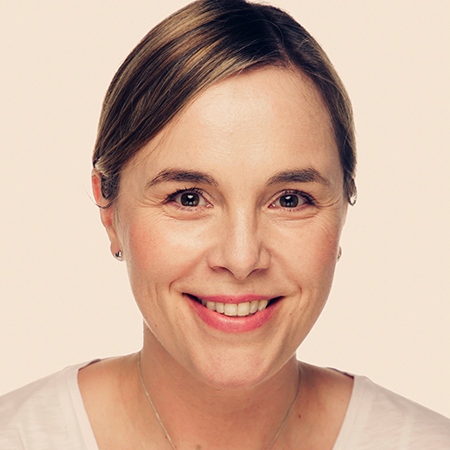
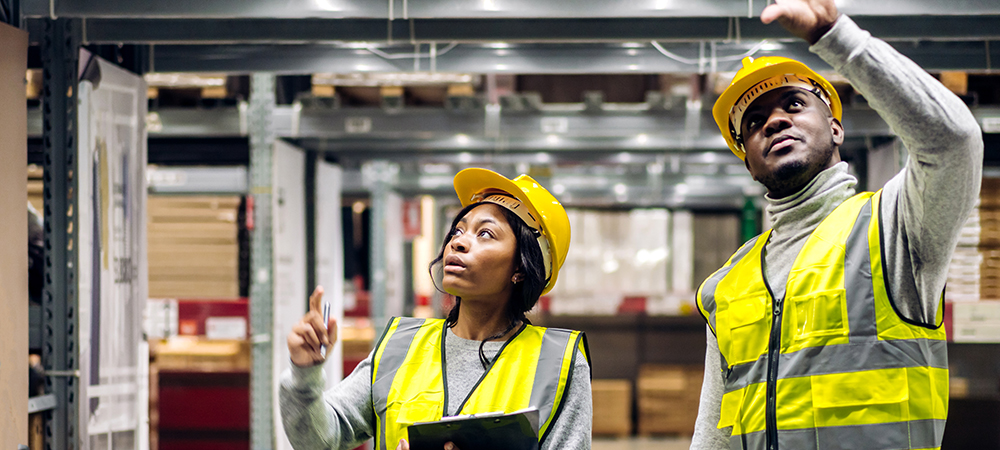
Early adopters and laggards
In an IFS, IDC study manufacturers were asked to self-assess their digital maturity. The study found that 75% consider themselves as digitally mature. A study by McKinsey highlights that many manufacturers have not been able to move beyond pilot purgatory, meaning that they have not been able to scale successful pilot programmes or fully leverage new tools and technology to see meaningful returns, business outcomes.
The differences between the two study points to a shortfall in devising a true long term and business wide vision on the value digital transformation can bring.
62% of manufacturers are struggling to articulate digital technology ROI which if deployed in siloes is to be expected. Manufacturers must start re-evaluating their digital transformation strategies to prevent further depletion of their investments and efforts. This will require focusing on real business needs, use cases and challenges, and integrating pilots into their mainstream business processes and roll these out across the wider manufacturing network.
Arrival of AI
As manufacturers continue their digital transformation journeys the amount of data that is now available has increased exponentially. AI and machine learning are allowing manufacturers to make smarter, more accurate and actionable decisions, enabling a standard production line, to become more autonomous as each moving part can think independently and acts on future information like weather forecasts and consumer spending habits.
“It is this smart way of thinking that is allowing manufacturers to become leaner and more agile, and crucially home in on their customer centricity strategy,” points out IFS’s Slowik.
For many that are on the AI journey benefits are already visible; for those that are just starting out it can be a daunting task knowing where to begin, with questions such as do you make your legacy factory smart, do you add sensors to warehouses or look at using algorithms to predict consumer habits? There may be an opportunity to first consider AI to help guide the decision.
Process or discrete manufacturers, or a hybrid of both, are being forced to rethink how they operate. The reality is that the current levels of uncertainty created by geopolitical events, supply chain disruptions locally and globally and the ensuing reactive consumer behaviour are not making this a question of if but when.
A clear certainty is that resilience, agility and adaptability are technology dependent to allow companies to stay preforming relevant and profitable.